Sorry, this entry is only available in French.
Category Archives: blender
Nouvelle édition de Blender pour l’architecture
Yaph 3: Yet Another 3D Printed House n°3
A new test of the use of displace modifiers in Blender to generate some forms and shapes suited to 3D printing. I used for this model the BronzeFill filament from ColorFabb. I printed it in the fablab Chantier Libre. It gives after sanding a very hard, heavy and shiny material that definitely does’nt look like plastic.
You can download the .blend file frome here.
In this video you can see the whole process from modeling in Blender to sanding:
Soutenons le projet de film libre Gooseberry
C’est la dernière ligne droite pour soutenir le projet de long métrage d’animation libre Gooseberry porté par la fondation Blender.
Toutes les données du film seront sous licences libres et ce sera l’occasion de développements exceptionnels pour le logiciel libre de 3D Blender.
Vincent Mabillot a déjà traduit les différentes possibilités de soutient, que nous recopions ici sans son aimable autorisation mais je pense qu’il nous pardonnera:
Si vous n’êtes pas pote avec l’anglais dans le texte, un petit résumé des propositions de financement:
- Ce que vous voulez (pledge a custom amount) : gratitude spirituelle du projet
- 20€ Téléchargement du film en avant première et réduction de 20euros sur la commande « support rigide » (Dvd, BluRay…)
- 45€ Blender Cloud – Now : Même chose que le précédent mais en plus activation d’un compte « Blender Cloud » (pour profiter de la plate-forme de création et partage) et en suite un financement mensuel de 10€ pendant les 18mois du projet
- 45€ Blender Cloud – Pledge : pareil que celui d’avant sauf que le compte n’est activé que lorsque la cible de la campagne de financement est atteinte.
- 175€ Film Credit : Ton nom au générique
- 195€ Cloud + Credit – Pledge : même principe que précédemment avec un démarrage sur la réussite de la campagne
- 450€ Bronze Sponsor Credit : au générique et sur le site web avec les sponsors Bronze
- 900€ Silver Sponsor Credit : genre Bronze mais en plus gros
- 2500€ Gold Sponsor Credit : Là on aura le temps de te reconnaître (sans loupe)
- Ce que tu veux en énorme…
Displace modifier experiments
This is a short video I presented during the LGM2014.
It uses some displace modifier with animated procedural textures.
You can download the blend file on the following link (licence CC-by-SA):
Tricube House is on the cover of the special issue of Eco-Maison-Bois
A double page about the Tricube house has been published in a special issue of Eco-Maison-Bois.
The 3D image made with Blender to explain the technical structure is on the front cover:
3D print for architects
A lot is said about 3D printing and how it may change (or not) the world. As an architect I will try to show you how it can change the way you think about physical models of your designs. After more than ten years of use of Blender for building virtual buildings (that sometimes are build in real life after 😀 ), to be able to print those designs right on my desktop is realy exciting. So here are some examples of how 3D printers can be used for architectural projects, and some practical aspect of 3D printing with FDM for architectural designs.
Several technologies exist for 3D printing, but the most widely used is Fused Deposition Modelling (FDM), thanks mainly to the RepRap project. An extruder heat a filament and deposit it layer by layer to create the shape. The material is generaly PLA (a biodegradable plastic) or ABS. Some technics allow much higher quality, wider range of material and color printing, and you can use the services of some websites to have your projects printed at some cost. But here I will speak of the FDM, the only technic that one can buy for himself. One can build its own 3D printer for around 500$ or even less, or buy a kit or a complete 3D printer for less than 2000$. The different models have different speed, reliability and precision.
At Chantier Libre, the FabLab I’m lauching we bought an Ultimaker, as it is known to be very fast and accurate, and to be useable easily without too much tinkering. But the main reason is that it is OpenHardware.
The thing I prefer with 3D printing is that it allows you to create shapes you could not build with traditionnal technics. As an example I used for that again a softbody simulation to generate the geometry, and a decimate modifier to make a polygonised “low-poly” version of it. It is inspired by the work of Gaudi:
After modelling in Blender, you export the model in STL format, and open it in CURA, the software that will change this model to something understandable by the printer. In Cura you can resize, move and rotate your model, and then slice it: it will calculate each layer of material that will be deposited by the printer. You can choose the speed, the temperature, the thickness of the walls, the density of the fillings…
A timelapse of the whole process:
For simple forms, the quality is good with the default settings of the software, no need for hours of experimentations. You have to cope with the typical FDM surface : you can see the layers of PLA (but with high quality settings, and a layer height of 85 micrometers, it’s not so much a problem). You can after that sand the model like in the example below, or use some new filaments that leave a sandstone like surface (I’m testing it right now):

For more complex forms like the ones in the video, you may need to add supports (the software places them for you) for the hangover. In some cases, you may need to adjust the settings (like for the columns of the example) to prevent some small blobs or wires. And like every tool, the more you know it, the bertter you use it. For such complex models, the use of the 3D print tool box included in Blender really can help you out sparing a lot of time .
The most annoying part is the time needed to print. A small objects of less than 3cm can be printed in less than 10 minutes, like the ones below:
But a big object like the example takes easily 20 hours to print. Don’t forget we work in 3D: 3 times larger means 27 times longer. So you can easily understand you are not so much limited my the size of the printer (it can print 20cmx20cmx20cm) but by the time.
I may say to finish that today, with a reasonably preiced printer you can achieve some very nice results, and it allows you to design shapes you could not imagine build before. But don’t forget this technology is still young : it takes some time, it’s not perfect, and the printer itself will give its best result only if you spend time to master it. And thats why FabLabs are so great: the fab managers master the tools for you and help you get the best of your 3D models.
Here you can download the .blend file:
cathedrale
Or directly the two stl files to print them:
cathedrale
cathedralefacettes
Capitole du Libre à Toulouse les 24 et 25 novembre 2012 : ateliers et conférences
Conference and workshop about Blender for architecture in Lyon november the 18th
I will give a conference and a workshop in Lyon for the JDLL the 18th of november.
Blender conference 2012
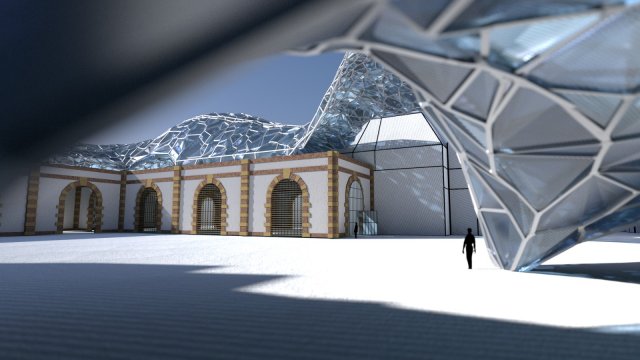
For the 2012 Blender Conference, I gave a presentation of my use of Blender as a design tool.
Here is the video of the conference, unfortunately with low resolution:
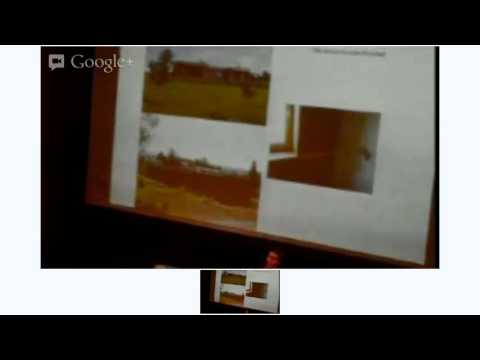
Here is the PDF of my slides for the conference, with better quality images it’s about 10 megas
The SVG version ca be opened in any modern browse. It’s heavier, about 20 megas, so you may prefer right click > save as:
And here are two videos of previous works I used for the presentation: